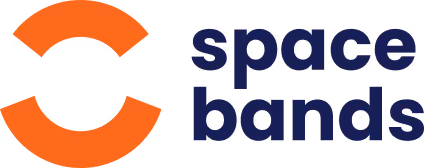
spacebands is a multi-sensor wearable that monitors external, environmental hazards, anticipates potential accidents, and gives real-time data on stress in hazardous environments.
Sign up to the mailing list:
Subscribe
I’m Arianna, founder of Syncra Group and EHS Tech Connect. I’m a voice in the EHS systems, software, technology and data community. I help companies build EHS digital systems that actually work—connecting people, tools, and data to drive outcomes that matter.
I started in EHS with boots on the ground—fieldwork, safety meetings, inspections, all of it. Then I moved into consulting, where I became a bit of a jack-of-all-trades: auditing programs, chasing findings, building reports. That’s when I stumbled into EHS systems—not as a strategist, but because I was tired of doing things the long way.
Once I saw how the right tech could actually make the work easier, I was hooked. I eventually took that experience in-house, leading EHS IT from within a company. That’s where I saw the other side: the ownership, the budget pressure, the cross-functional politics—and the reality of expensive systems that no one is using. That accountability changed how I think about systems entirely, and it made me want to help others avoid the same slow, frustrating lessons.
It’s why I launched EHS Tech Connect—to share what I’ve learned with other EHS leaders and build a space where people can get smarter about systems without the vendor spin. And it’s why I started Syncra Group—a boutique consultancy to help businesses get this work right from the start. We lead digital strategy and roadmapping, guide software selection, manage implementations, streamline workflows, improve reporting, and step in as fractional EHS IT when needed.
We also advise EHS software vendors on how to build tools that people actually want to use. Whether you’re trying to fix what’s broken, build something better, or bring a product to market that truly fits the field—we help you close the gap between intent and impact.
Digitization without definition leads to dysfunction. One of the most common traps in EHS digitization is assuming a system will fix a process problem. In reality, digital systems will just amplify whatever exists—clarity or confusion.
If there’s no clear expectation, policy, or training behind a process, automation will just make the dysfunction faster and more visible. Take action item closure as an example. Before layering on system-driven escalations, ask: Have we clearly communicated that actions must be closed in 30 days? Is that policy written, trained, and understood?
Only after that’s in place should the system be configured to support it. Don’t digitize ambiguity. Define first—then digitize.
The real difference between a scalable EHS platform and a short-term fix is what’s under the hood—and who can touch it. A truly scalable system won’t fall apart when you add a new field or introduce more complex hierarchies. Data model flexibility matters. If the system can’t adapt without breaking, it’s not built to last.
More importantly, you shouldn’t need a statement of work to add a dropdown. If every tweak requires vendor involvement, your system might be customizable, but it’s not configurable—and that distinction matters. Scalable platforms empower internal system admins to iterate, test, and evolve without opening a ticket every time.
Knowing who controls future changes—and how easily those changes can be made—will save a lot of heartache (and budget) down the road.
EHS—always. It’s 2025. IT teams are already deep into conversations about AI agents, automation, and system integration. Most are eager for business units to be self-sufficient with the right off-the-shelf tools. While it can take coordination, IT generally values structure, governance, and clear ownership. With the right framing, alignment is possible—and often welcomed.
The harder part is within EHS itself. New systems don’t just replace tools; they challenge long-standing habits, “we’ve always done it this way” isms, decade old spreadsheets, and processes that inadvertently live in people’s heads. Even when there’s a better way, change brings uncertainty. That’s why communication, training and change management is the most critical piece in any system implementation—big or small.
Success isn’t just about what the software can do, but how well it’s understood, adopted, and trusted by the people who use it every day. Bring them in early. Give them a voice. Let them take pride and ownership in the system they help shape.
Success isn’t just about what the software can do, but how well it’s understood, adopted, and trusted by the people who use it every day.
Here are a few best practices to help with this hurdle:
Yes—during one implementation from a legacy EHS system, we had initially planned to launch a standalone incident reporting form. It was simple, modern, and a clear upgrade from what the old system offered.
But in the lead-up to go-live, someone from ops who was on the feedback team pointed out, “Why not just put it in the same place we already submit IT tickets and HR requests?” It was a good call.
The company already had an intranet ticketing portal that employees used daily—for onboarding, tech issues, payroll questions. Embedding the incident and hazard concern forms there made the process more intuitive and accessible without adding another system to learn or link to remember.
That feedback shifted our approach: instead of prioritizing a clean standalone tool/URL, we prioritized visibility and ease of access. It’s a small decision that made adoption smoother right out of the gate.
It’s helping EHS teams and vendors understand each other’s world. They’re both trying to make the system work, but they come in with different assumptions and priorities. Vendors aren’t the ones holding the bag when the system doesn’t deliver—when metrics are off, adoption lags, or leadership is frustrated.
They focus on their product roadmap, making the system work for dozens or hundreds of customers and being agile. EHS teams often underestimate what goes into what seems like a “quick change.” Behind the scenes, it might involve multiple environments, dependencies, or impact other clients on the same platform.
My role is to bridge that gap. I push vendors to stay connected to the real-world business impact, and I coach EHS teams to be clearer about priorities, constraints, and tradeoffs. Making sure EHS teams have clear processes in place before expecting a digital change and making sure vendors understand the “why” behind an ask.
Most EHS software integrations don't hit a wall because the technology doesn’t work, but because the underlying data doesn’t line up. Administrative data is usually the first issue. HR uses one naming convention for departments, EHS uses another. Is a “location” a single building or an entire site? Assets might be managed in one system and referred to differently on the floor.
These inconsistencies create chaos in reporting and make it nearly impossible to get clean insights across systems.
The other common mistake is assuming the user-facing interface reflects how the data is structured behind the scenes. It doesn’t, usually. Field names, table organization, and overall data quality vary widely across platforms.
If you’re planning to push this data into a warehouse or BI tool, those details matter. So don’t just ask about workflows—ask how the data is organized, what’s exposed, and how integrations are handled. If you can’t get clear answers, that’s your signal.
Design forms and workflows around work-as-done, not work-as-imagined.
If your categories, picklists, or workflows don’t reflect how people actually talk and work in the field, you’re not going to get meaningful data—you’re going to get check the box submittals.
If “Other” keeps showing up, that’s a signal, not noise. Revisit your options. You may need to simplify, reword, or remove what isn’t adding value. Not every data point is worth collecting—focus on what drives action.
The goal isn’t to track everything—it’s to surface what matters. Clean, relevant inputs lead to insights you can act on. The rest is just distraction. Most modern EHS software have regulatory requirements/ best practices built in, leverage that out of box expertise and focus on configuration that aligns with your business.
All of these technologies—AI, wearables, computer vision—have made fast progress. You can go to almost any vendor’s website and see recognizable logos from high-risk industries. The tools are out there, and they’re working in a lot of cases. But the biggest leap won’t come from more tech—it’ll come from connecting the dots. Right now, most of these tools are being used in isolation. Data isn’t centralized, systems don’t talk to each other, and insights stay siloed.
The next shift will be about building cohesive, feedback-driven systems that adapt in real time to changing risk. For example: a worker flags a hazard using voice input on a mobile app. A nearby camera uses computer vision to confirm the condition.
The system checks it against recent reports and updates the site’s risk profile, flagging an increase in frequency and severity for that task. Supervisors are notified, the issue is added to the corrective action tracker, and it’s brought into the next safety meeting for discussion.
That’s not a flying cars futuristic vision—the pieces already exist. We just need to connect them.
Oh man, what a loaded question. Honestly, I wouldn’t start with tech at all. I’d start with the basics: What’s getting in the way of safer, more efficient work? What’s slowing people down, what’s getting ignored, and what’s falling through the cracks? Then I’d build around fixing that.
And no, it’s not about shiny new tools. It’s about having good systems in place—solid, connected, and built to last. If the foundation is strong, you can layer on the cool stuff without it falling apart
Five years from now, the strongest EHS leaders will be the ones who can connect the dots—between risk and operations, between frontline work and business priorities, and yes, between systems and strategy.
The core of the role remains the same: protect people, ensure compliance, lead culture. But the context is shifting.
Top performers won’t just be experts in safety—they’ll also be skilled communicators, trusted cross-functional partners, and increasingly fluent in how their work connects to systems, workflows, and business performance.
Now, that doesn’t mean every EHS VP needs to be a data systems architect. But their executive peers in Operations, HR, and Finance are already working with highly technical teams, shaping roadmaps, and making decisions based on integrated data and enterprise systems.
EHS has historically been a step behind in those conversations—whether it’s about system design or capital investment—and that gap is starting to show. The next generation of EHS leaders will still lead with field credibility, but they’ll also know how to spot broken workflows, ask sharper questions about tools, and make sure safety is fully at the table when the business is talking about performance, investment, and risk.
You can reach Arianna on LinkedIn here - https://www.linkedin.com/in/ariannabhoward/
We think you'll also find the articles below really useful
Join 5,000 H&S professionals and sign up for the spacebands monthly newsletter and get the latest blogs, free resources, tools, widgets and a dose of health & safety humour.
spacebands is a multi-sensor wearable that monitors external, environmental hazards, anticipates potential accidents, and gives real-time data on stress in hazardous environments.