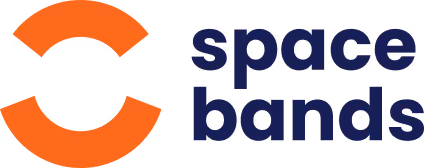
spacebands is a multi-sensor wearable that monitors external, environmental hazards, anticipates potential accidents, and gives real-time data on stress in hazardous environments.
Sign up to the mailing list:
Subscribe
Hand arm vibration (HAV) is a significant workplace hazard, caused by operating hand-held power tools like road breakers, grinders, and lawnmowers.
Prolonged exposure to these vibrations can lead to Hand-Arm Vibration Syndrome (HAVS)—a painful, often irreversible condition affecting circulation, nerves, muscles, and joints.
This guide will show you how to measure hand arm vibration exposure, comply with the Control of Vibration at Work Regulations 2005, and protect your workforce from long-term harm.
These regulations aim to protect workers from the risks of HAV by setting legal limits for exposure and requiring employers to take actions to prevent or control exposure.
Measuring HAV exposure is essential for assessing the level of risk and determining the appropriate control measures.
However, measuring HAV exposure can be challenging, as it depends on various factors, such as the type and condition of the tool or equipment, the duration and frequency of use, the way the worker holds or operates the tool or equipment, and the characteristics of the work or material.
Therefore, this blog will explain some of the methods and tools that can help employers and workers measure HAV exposure accurately and effectively.
If you're interested in this article you may also be interested in our HAVS Toolbox Talk, HAVS in Construction, Manufacturing and Logistics, and HAV Compensation.
According to the web search results, the history of hand-arm vibration syndrome (HAVS) dates back to the early 20th century, when it was first recognised as an occupational disease among workers who used pneumatic hammers and drills.
The term “vibration white finger” was coined in 1911 by Loriga, who described the blanching and numbness of the fingers in Italian quarry workers.
The condition was also observed in other countries, such as Japan, Germany, and the UK, where it was known as “dead finger”, “Raynaud’s phenomenon of occupational origin”, or “occupational acroparaesthesia” respectively.
In 1975, the International Labour Organization (ILO) adopted a resolution to classify HAVS as an occupational disease and to establish diagnostic criteria and compensation schemes.
The term “hand-arm vibration syndrome” was introduced in 1986 by the Stockholm Workshop on Vibration-Induced Disorders, which recognised that HAVS can affect not only the vascular system, but also the sensory and musculoskeletal systems of the hand and arm.
Since then, HAVS has been widely accepted as a generic term for the various disorders caused by exposure to hand-transmitted vibration.
HAVS is diagnosed based on the symptoms and exposure history of the worker, as well as a physical examination and some tests.
The symptoms of HAVS are classified into three stages: vascular (affecting the blood circulation), sensory (affecting the sensation) and musculoskeletal (affecting the muscles and bones).
The stages are further divided into early and late sub-stages, depending on the severity and frequency of the symptoms. The diagnosis of HAVS is confirmed by the presence of IgM antibody to HAV in the blood, which indicates an acute infection.
There is no specific treatment for HAVS, but the condition can be prevented or improved by stopping or reducing exposure to vibration.
One of the key factors that determines the level of HAV exposure is the vibration magnitude of the tool or equipment. The vibration magnitude is a measure of the intensity of the vibration, usually expressed in metres per second squared (m/s²).
The higher the vibration magnitude, the higher the risk of HAVS. Another factor that affects the HAV exposure is the exposure duration, which is the total time that the worker is exposed to the vibration in a day. The longer the exposure duration, the higher the risk of HAVS.
To assess the risk of HAV exposure, it is important to compare the vibration magnitude and exposure duration with the legal thresholds set by the Control of Vibration at Work Regulations 2005.
These thresholds are called the exposure action value (EAV) and the exposure limit value (ELV). The EAV is 2.5 m/s² and the ELV is 5 m/s².
These values represent the daily vibration exposure that a worker can be exposed to without significant risk of injury.
If the vibration exposure exceeds the EAV, then employers must take actions to reduce it. If the vibration exposure exceeds the ELV, then employers must take immediate actions to prevent further exposure.
If measuring EAV and ELV seems quite complicated to you, you wouldn't be the first to think so. In fact, it's one of the reasons spacebands developed a HAV monitoring feature into our workplace wearable. It allows employers to set threshold levels they are comfortable with (out of the box spacebands' devices are set to HSE regulations), and allow workers and employers to get on with their jobs without having to worry about complicated calculations.
To measure vibration magnitude and exposure duration, there are several methods that can be used, such as using a vibration meter, consulting manufacturer’s data, or using online tools like the HSE vibration calculator.
Each method has its own advantages and disadvantages, and some tips for choosing the most suitable one for different situations are given below.
The exposure points system and the ready-reckoner table are tools that can help estimate HAV exposure from multiple sources or tasks.
The exposure points system is a way of expressing HAV exposure in terms of points, where 100 points is equivalent to the EAV of 2.5 m/s² and 400 points is equivalent to the ELV of 5 m/s².
The ready-reckoner table is a table that shows the number of points for different combinations of vibration magnitude and exposure duration. To use these tools, follow these steps:
Here are some examples of what that might look like in an actual business case:
A carpenter uses a circular saw, a hammer drill, and a sander for different tasks in a day. The manufacturer’s data for these tools are as follows: circular saw: 4 m/s², hammer drill: 15 m/s², sander: 2.5 m/s². The carpenter uses each tool for 30 minutes in a day. To calculate HAV exposure, follow these steps:
A gardener uses a hedge trimmer, a leaf blower, and a lawn mower for different tasks in a day. The gardener does not have any manufacturer’s data or vibration meter for these tools, so he uses an online tool like the HSE vibration calculator to estimate the vibration magnitude and exposure duration.
The online tool gives him these results: hedge trimmer: 5 m/s², 15 minutes; leaf blower: 3 m/s², 45 minutes; lawn mower: 2 m/s², 60 minutes. To calculate HAV exposure, follow these steps:
Some actions that employers and workers can take to reduce HAV exposure are:
HAVS claims are compensation claims made by workers who may or may not have developed HAVS as a result of their work.
At spacebands we regularly speak with companies that have had to pay out on fraudulent HAVS claims because even if an employee hasn't been over-exposed to hand-arm vibration, it's hard to prove in a court of law.
At spacebands, our wearable tech simplifies hand arm vibration monitoring. With real-time alerts and automated reporting aligned to HSE exposure limits, employers can confidently manage HAVS risk and defend against false claims. Book a demo to see it in action.
Check out our article on Hand Arm Vibration Compensation Claims for more information on protecting your business.
We think you'll also find the articles below really useful
Join 5,000 H&S professionals and sign up for the spacebands monthly newsletter and get the latest blogs, free resources, tools, widgets and a dose of health & safety humour.
spacebands is a multi-sensor wearable that monitors external, environmental hazards, anticipates potential accidents, and gives real-time data on stress in hazardous environments.