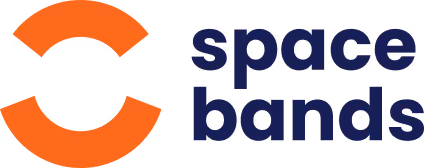
spacebands is a multi-sensor wearable that monitors external, environmental hazards, anticipates potential accidents, and gives real-time data on stress in hazardous environments.
Sign up to the mailing list:
Subscribe
Download your toolbox talk by clicking the button above and print it off to deliver to your team.
Before we get started on our manual handling toolbox talk, did you know spacebands have a whole range of toolbox talks on different subjects which we add to regularly, don't forget to bookmark the page. You can (and should) sign up to our newsletter and we'll deliver our toolbox talks and lots of other useful free content straight to your inbox.
We think you'll also find the articles below really useful
Join 5,000 H&S professionals and sign up for the spacebands monthly newsletter and get the latest blogs, free resources, tools, widgets and a dose of health & safety humour.
spacebands is a multi-sensor wearable that monitors external, environmental hazards, anticipates potential accidents, and gives real-time data on stress in hazardous environments.